Some Ideas on Lean Manufacturing You Should Knows
Wiki Article
Plastic Manufacturing - Questions
Table of ContentsSome Known Details About Plastic Manufacturing The Greatest Guide To OemMfg - TruthsLittle Known Questions About Plastic Manufacturing.
With shot moulding, pre-dried granular plastic is fed by a forced ram from a receptacle into a heated barrel. As the granules are gradually relocated onward by a screw-type bettor, the plastic is compelled into a heated chamber, where it is thawed. As the bettor advances, the thawed plastic is required through a nozzle that relaxes versus the mould, enabling it to go into the mould tooth cavity through a gateway and also runner system.The series of events during the shot mould of a plastic part is called the shot moulding cycle. The cycle begins when the mould shuts, followed by the shot of the polymer into the mould dental caries. When the tooth cavity is loaded, a holding stress is kept to compensate for product shrinking.

Once the cavity is 98% full, the machine switches from velocity control to pressure control, where the cavity is "packed out" at a constant pressure, where sufficient velocity to reach desired stress is called for. This allows employees regulate component dimensions to within thousandths of an inch or much better. Various sorts of shot moulding procedures [modify] A lot of injection moulding procedures are covered by the traditional procedure description above, there are numerous vital moulding variants including, but not restricted to: A more extensive list of shot moulding processes might be located right here: Process repairing [ modify] Like all industrial procedures, injection molding can produce mistaken parts, even in playthings.
Oem - An Overview
Trials are commonly executed prior to complete manufacturing runs in an initiative to anticipate flaws and also establish the ideal requirements to make use of in the shot process.: 180 When loading a brand-new or unknown mould for the very first time, where shot size for that mould is unknown, a technician/tool setter might perform a trial run before a complete manufacturing run.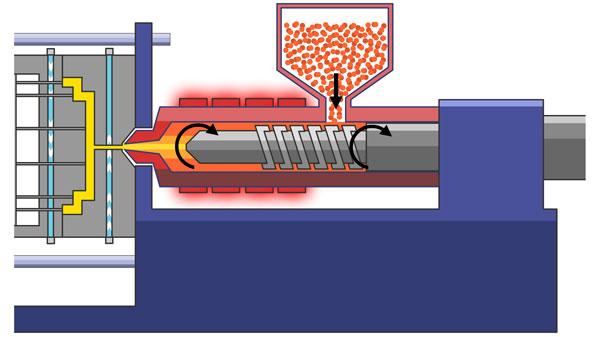
Holding pressure is raised up until the parts are cost-free of sinks as well oem manufacturing as part weight has actually been achieved. Molding problems [edit] Shot moulding is a complex modern technology with feasible production troubles. They can be triggered either by defects in the moulds, or regularly by the moulding process itself.: 4785 Moulding issues Alternative name Summaries Causes Sore Blistering Raised or split zone on surface of the component Tool or product is too warm, often triggered by a lack of cooling down around the device or a defective heating system.
The Main Principles Of Lean Production
Installed particulates Foreign bit (burnt material or various other) ingrained in the part Particles on the device surface area, polluted product or international debris in the barrel, or excessive shear warmth burning the material before injection. Circulation lines Directionally "off tone" wavy lines or patterns Injection speeds also slow-moving (the plastic has cooled off way too much during injection, shot rates should be set as quick as is ideal for the process and material utilized).Loading too fast, not allowing the sides of the part to establish. Mould might be out of enrollment (when the two halves don't centre appropriately and also component wall surfaces are not the very same density). The provided information is the common understanding, Modification: The Lack of pack (not holding) pressure (pack pressure is utilized to pack out even though is the part during the holding time).
In other words, as the part shrinks the material separated from itself as there was not sufficient resin in the cavity. The space might occur at any type of area or the part is not limited by the thickness yet by the material circulation as well as thermal conductivity, however it is a lot more likely to occur at thicker areas like ribs or bosses.
Knit line/ Meld line/ Transfer line Discoloured line where 2 flow fronts fulfill Mould or material temperatures set as well low (the product is chilly when they meet, so they do not bond). Time for shift in between injection and also transfer (to packaging and also holding) is too very early. Twisting Distorted component Air conditioning is as well brief, material pop over to this site is also warm, absence of cooling around the tool, incorrect water temperatures (the components bow inwards towards the hot side of the device) Uneven reducing in between locations of the part.
Our Oem Ideas
125 inch wall thickness is +/- 0. The power required for this process of injection moulding depends on many points and also differs in between materials utilized. Below is a table from web page 243 of the same recommendation as previously pointed out that finest shows the qualities appropriate to the power required for the most commonly used products.In enhancement to placing assessment systems on automated gadgets, this contact form multiple-axis robots can get rid of parts from the mould as well as position them for more processes. Specific instances consist of removing of parts from the mould right away after the parts are created, along with using device vision systems. A robot grasps the component after the ejector pins have been included release the part from the mould.
Why is shot molding machine production so effective? What is Shot Molding?
The shot molding maker makes use of custom-made molds to fill them out according to specifications, developing the same duplicates that can be customized in a selection of ways. What's even more, shot molding is an extremely functional process, enabling a wide variety of various materials as well as coatings, which makes it a prominent alternative in countless markets with entirely various goals as well as needs - manufacturing.
Report this wiki page